Conveyors vs. Trucks: How to Reduce Costs in Material Handling
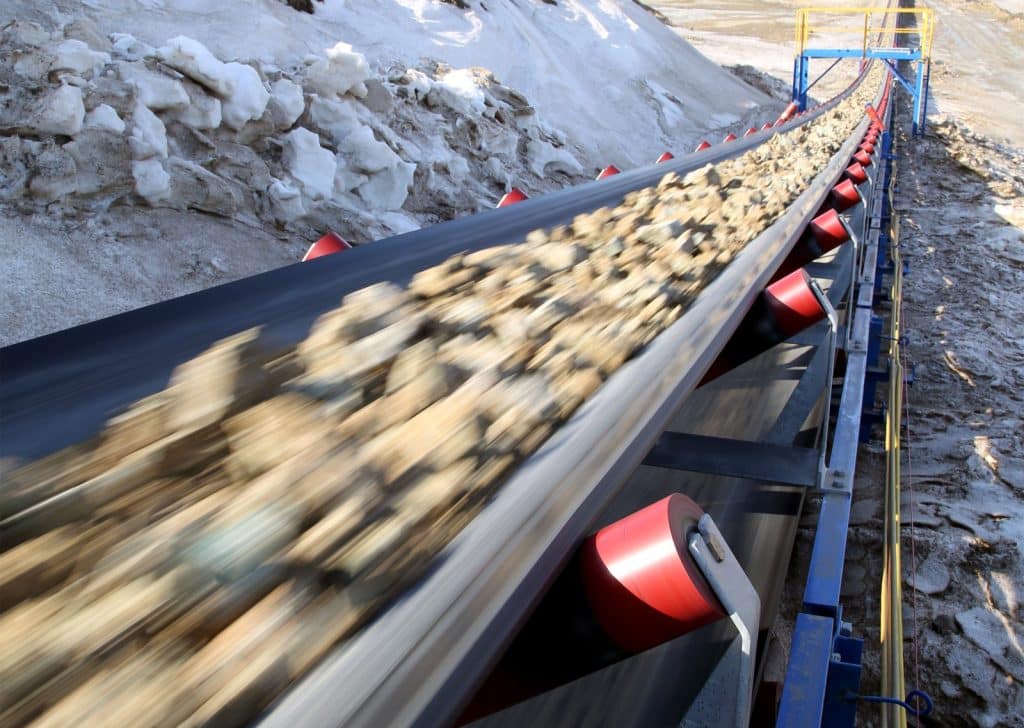
Conveyor systems and short-haul truck fleets remain the most popular and effective ways to move large amounts of bulk materials at many mining, construction, and processing operations. In this article, we take a close look at how choosing the solution for your construction, mining, or processing operation can help you control and lower costs over the lifetime of your project.
This article includes:
- A comparison of capital and operational costs for conveyors vs. haul trucks
- Case Study: Comparing conveyor vs. haul trucks costs at a Brazilian iron ore mine
- Efficiency, reliability and safety of conveyors vs. haul trucks
- Environmental and sustainability considerations
- Conclusions and recommendations
INTRODUCTION: A MOVING TARGET
If you’re planning to or are currently running a large construction or mining project, you already know that just getting bulk materials to where they’re needed is going to eat up a huge chunk of your budget.
Estimates vary widely according to terrain, distance, project duration, and the type of materials being moved. One study of material transport costs across all types of construction projects found these could often comprise 40-60% of total expenditure.
This paper will focus specifically on challenges and potential solutions for reducing materials handling costs in big mining and construction projects. Considering the unique challenges these projects face, including heavy materials, long transit distances, and extreme terrain, it is likely material transport costs on these projects would fall on the higher end of that range.
Whatever that number might be for your project, choosing the right materials handling option is a critical decision. We’ll look in detail at the two major options for moving bulk materials: diesel-powered haul truck fleets and conveyor systems.
TRADITIONAL TRUCKING: READY TO ROLL
Fleets of heavy-haul trucks are traditionally the go-to option, especially for complex construction projects with multiple points of delivery. The appeal is clear because truck fleets offer:
- Flexible operations
- Low initial costs
- Scalable operations
- No long-term commitments
However, the common notion that trucks are the low-cost, low-commitment option is increasingly being challenged by higher operational costs, including rising fuel and maintenance expenses and a long-term shortage of qualified drivers.
There’s also growing awareness of the environmental costs of operating large numbers of heavy-haul vehicles over the long term, as well as the impact these fleets have on the communities in which they operate including safety challenges, increased noise, and damage to roads and public infrastructure.
CONVEYOR SYSTEMS: ESTABLISHED IDEA, EMERGING POSSIBILITIES
Often perceived as inherently less flexible than haul trucking and coming with higher set-up costs, conveyor systems are gaining ground outside their traditional stronghold in the mining and bulk extractive sectors. More companies are looking seriously at the advantages conveyor systems offer, including:
- Continuous operation
- All-weather service
- Improved safety
- Reduced labor requirements
- Compatibility with renewable energy supply.
It’s a movement that’s powered by innovation in conveyor design, including portable systems that can be moved or repositioned as project needs changed and regenerative equipment that uses variations in the terrain to lower energy consumption.
Below we take an in-depth look at how haul trucks and conveyors stack up, including:
- Capital vs operational costs
- Reliability, downtime, efficiency, and safety
- Suitability for different projects
- Environmental considerations
1. CAPITAL VS. OPERATIONAL COSTS
As a manager or procurement specialist, you’re responsible for balancing capital and operating costs over the life of your project. While much depends on the duration of your project, if you’re going to haul materials for more than a few months, it’s important to balance potential upfront savings against returns on a more sustained investment.
TURNKEY OR TENURE: ASSESSING INITIAL COSTS
Haul truck fleets are usually ready to roll as soon as you are, offering a far lower entry price point to bulk hauling. They’re also easy to fund as a line item in your operational budget. Contractors can be hired when you need them and trucks can be idled during construction slowdowns or operational delays. Fuel and maintenance costs are high but relatively predictable if you own your trucks (at least in the short term) and not your concern if you don’t.
Conveyor systems will always require more planning and a more complex procurement and set-up process. They also may simply be unsuitable for projects with moving pick-up or delivery points. While portable or moveable conveyors may provide an “out of the box” solution on some sites, initial and short-term costs will almost always be higher for conveyor equipment, and will usually require a significant upfront capital commitment.
How much? Engineers suggest design and installation of a new conveyor usually starts at around $75,000 while a ballpark figure for a basic two-mile line connecting a mine to a preparation site might cost $2-3 million.
DOWN THE ROAD: LONG-TERM EXPENSES AND SAVINGS
This division starts to break down on bigger and longer projects. Contractors on long-term projects will build more maintenance and depreciation costs into their terms and bigger projects will require specialized haulage equipment that might be harder to source. You’ll also be exposed to fluctuations in fuel costs.
By contrast, these longer-term expenses tend to come down as a portion of total project expenditure for conveying equipment. Conveyors are far more energy-efficient than haul trucks and once installed, typically require less maintenance per tonne of material moved over the same distance.
If you’re moving significant amounts of material between fixed points for any extended period of time, conveyors quickly begin to make sense.
INDUSTRY DISRUPTOR: LABOR COSTS AND THE DRIVER SHORTAGE
Rising labor costs and a systemic shortage of qualified heavy-haul drivers pose a long-term challenge and potentially disrupting force within the mining and construction industry. While it’s hard to split out numbers for drivers of shorter-haul trucks carrying bulk materials, the American Trucking Association estimates the industry as a whole is short about 64,000 drivers. Although higher wages are providing some relief, many more drivers are retiring or are leaving the industry than are joining it.
Many large-scale open-cast mines are moving ahead with driverless computer-controlled haul trucks but for most operators, the driver shortage is a problem that is here to stay. At the same time, higher wages and increased labor costs for workers to load, unload, and maintain trucks are increasing costs for haul fleets. Conveyor systems, by contrast, operate continuously with automated loading and unloading with far lower labor requirements. In fact, on average, conveyor operations require only half as many workers as a truck haul operation of comparable size.
2. CASE STUDY: TRUCKS VS. CONVEYORS AT A BRAZILIAN IRON ORE MINE
Differences in application and scale make generalizations about the relative costs of haul trucks and conveyors difficult. However, a study at the Fabrica iron ore mine in Brazil shows how the costs and relative viability of haul tracks and conveyor belts stack up in one specific case. The study compared the capital costs of supplying specialist off-road trucks to haul ore to one, two, or three crushing units versus installing three alternative conveyor systems to serve the same crushing unit configurations. The research also compared the operational costs of supplying all three crusher configurations with the same volume of ore. Capital investment was as follows, showing in each case that the cost of providing haul trucks was significantly below that of installing conveyor systems—but that the capital cost of serving the crushers increased with transit distance for both trucks and conveyors.
Capital Costs Comparison | ||||
---|---|---|---|---|
Alternative | No. of crushers | Conveyor Length | Conveyor Capital Cost | Truck Capital Costs |
A | 1 | 2,560m | $55 million | $12.5 million |
B | 2 | 4,660m | $56.6 million | $19.9 million |
C | 3 | 6,760m | $90.9 million | $53.8 million |
Meanwhile, operational costs measured as the total expense of moving ore by the tonne were steady for trucks in all three situations. By contrast, the cost of moving ore by conveyor, was in each case increasingly cheaper.
Operation Costs Comparison | |||
---|---|---|---|
Alternative | Conveyor Length | Conveyor Operating Cost ($/tonne) | Truck Operating Cost ($/tonne) |
A | 2,560m | 0.68 | 0.97 |
B | 4,660m | 0.44 | 0.97 |
C | 6,760m | 0.23 | 0.97 |
With production steady across all the alternatives, savings on individual alternatives were used to calculate a discounted cash for each method. These were then compared to generate the relative net present value added by conveyors vs. truck transport.
Net Present Value Added | ||
---|---|---|
Alternative | Conveyor Length | NPV Added by Conveyors |
A | 2,560m | -$16,980,401 |
B | 4,660m | $366,498 |
C | 6,760m | $26,564,712 |
The results show that for the shorter conveyors, trucking remained a more cost-effective method. But as transport length increased, the higher efficiency and lower cost per tonne of the conveyors significantly outweighed the cost to haul materials over the same distance by truck.
3. EFFICIENCY, RELIABILITY, AND SAFETY
While belt conveyors and trucks offer distinct cost trade-offs when compared head-to-head, there are many areas where the higher initial outlay on conveyor solutions may be justified by measurably higher efficiency, superior reliability, and a better safety profile.
EFFICIENCY
While head-to-head comparisons are useful for smaller projects, only conveyor systems provide the true bulk-handling capacity needed for the largest operations. Truck capacity tops out at 25 tonnes per trip for the largest road-ready vehicles. By contrast, an average-sized conveyor system can move 800 tonnes around the clock.
That means not only more material moving with less manual handling. It also means bulk-handling conveyors can deliver a cost-per-tonne dividend that truck fleets can never match. There have also been significant improvements in skirts, hoppers, and covers designed to minimize material loss, waste, and spillage.
Belts are capable of moving both wet and dry materials, as well as abrasive, sharp, and extremely fine materials including sand, gravels, ores, gypsum, and post-processing fines. They can handle loads with mixed clast or grain sizes very well. Trucks are preferred to appropriately designed conveyor belts only for moving loads containing very large rocks or stones.
FLEXIBILITY AND SCALABILITY
With no fixed infrastructure footprint, trucks are also a more flexible option than conveyors, able to shift load and unload points as your needs change and vary routes to suit local conditions. That flexibility is however limited by the relatively small load that an individual truck can carry.
Scaling a truck haul operation means putting more vehicles on the road, adding incrementally to fuel and maintenance costs, labor needs, and environmental impact. By contrast, our case study shows that operating costs fall as conveyor systems get bigger.
DOWNTIME
Conveyor systems have fewer separate moving parts than trucks which means they don’t break down as often. Other conveyor benefits include reduced wear, optimized loading, and continuous motion lets conveyors spend more time on the move than trucks and less time at a standstill due to maintenance and repairs.
Heavy-haul trucks often face restrictions on traveling after dark and the number of journeys per day through public areas. They can also be slowed down by traveling through congested urban areas. Even simply needing to cross one public highway can add significant delays over the lifetime of a project.
Fleets can also be halted by snow, ice, flooding, or extreme temperatures. Conveyor systems, on the other hand, provide a straight-line connection between the source and destination. They also operate 24 hours a day, seven days a week in all but the most extreme weather conditions.
SAFETY
Accidents and safety compliance add costs and increase downtime for trucking operations. Truck operations are also inherently dangerous. According to OSHA, approximately 75% of workplace struck-by fatalities involve heavy equipment such as trucks or cranes. Trucks also pose a potential hazard to the local community when they travel on public roads.
Modern conveyor systems run continuously with few workers directly accessing them during operation. Lines also typically run on private land far from public areas.
4. ENVIRONMENTAL AND SUSTAINABILITY CONSIDERATIONS
Improving the efficiency of hauling operations benefits not only the bottom line of your business but also the plant. Environmental responsibility, compliance, and social responsibility all support doing more to lessen the impact of hauling operations on the climate, local environment, and communities. We look at three key ways this can be done.
ENERGY INTENSITY
Materials handling is one of the most energy-intensive parts of many construction and mining projects. In fact, a study by the Department of Energy (DOE) found that in 2007, materials handling operations alone accounted for 17% of all the energy consumed by the mining industry.
Of this consumption, the same report found, roughly 87% could be attributed directly to diesel engines which are used predominantly to power heavy haul trucks.
ENERGY EFFICIENCY
Despite their prominence, diesel engines perform relatively poorly in energy efficiency, a measure of how much energy is lost compared to a theoretical minimum when completing a particular process. The DOE study found diesel engines used in materials handling average an efficiency of only 45%, with much older equipment still in use registering only about 30%.
Electrical engines—commonly used to power conveyors, stackers, and other fixed handling equipment—fared much better, with a typical value of 85%.
CARBON EMISSIONS
Diesel combustion engines powering haul equipment are major contributors to carbon emissions and have also been linked to fine particulate pollution that is considered particularly dangerous to the lungs of vulnerable people.
The Fabrica mine case study measured how increased reliance on electrically powered conveyor equipment reduced the average number of trucks needed on the project over the study period and resulted in a correlated reduction in carbon emissions as well.
SUSTAINABILITY
Changing to conveyor systems comes with other sustainability benefits including moving pollution away from populated areas and reducing the need to build new roads to allow trucks to access remote mining areas.
Conveyor systems are most likely to operate on electrical power, which not only reduces carbon emitted per tonne of material moved but is also easier to supplement with power from local renewable power sources including solar or wind.
The large power spike needed to get fully loaded conveyor belts moving remains a problem, as does the need for braking belts that are moving down steep slopes. However, innovative conveyor designs that “harvest” gravitational energy to help power systems are more common.
A study of a “regenerative” conveyor belt of this type installed at a Polish mine found the unit was able to move coal almost twice as efficiently as heavy haul trucks.
5. CONCLUSIONS AND RECOMMENDATIONS
Choosing an effective material handling solution for your construction or mining project is one of the most important decisions you will make. The right solution could save you tens to hundreds of millions of dollars over the lifetime of your operation.
The following table summarizes the major benefits offered by conveyor systems and haul trucks in terms of managing and controlling project costs. It also contains some general recommendations about which option might be best for your project.
Comparison: Conveyors vs Haul Trucks | ||
---|---|---|
Conveyors | Haul Trucks | |
Capital costs | High | Low |
Long-term operating cost | Low | High |
Lifetime maintenance costs | Low | High |
Downtime | Low | Higher |
Labor requirements | Low | Higher |
Load capacity | High | Limited |
Scalability | Good | Poor |
Speed | High | Low |
Material type | Almost Any | Any |
Flexibility | Low | High |
Safety | High | Low |
Energy efficiency | High | Low |
Environmental impact | Low | High |
Sustainability | Low | High |
Recommendations (✔️= Preferred) | ||
---|---|---|
Conveyors | Haul Trucks | |
Continuous operations | ✔️ | |
All-weather operations | ✔️ | |
Very large rocks | ✔️ | |
Longer distances | ✔️ | |
Shorter distances | ✔️ | |
Medium-to-large projects | ✔️ | |
Very small projects | ✔️ | |
Longer-term projects | ✔️ | |
Shorter-term projects | ✔️ |
Based on this general overview, it’s clear that short-haul truck fleets remain the best option for small- to medium-sized projects or very complex developments with multiple (and changing) pick-up and destination points, routes, and complex timelines. However, even these projects might find conveyor systems are effective for some limited applications.
Conveyors remain an effective and scalable option for many medium- to large-scale projects where large amounts of bulk materials need to be moved quickly and safely over established routes with minimal supervision, downtime, and maintenance.
That makes conveyors ideal for mines and bulk processing operations at ports or transit hubs. They’re also widely used on major, long-term construction projects. Talk to an experienced materials handling expert at a reputable equipment provider to find out which materials handling solution is best for your needs.
WEST RIVER CONVEYORS: SHIFTING EXPECTATIONS
At West River Conveyors, we build conveyor products that shift expectations about what’s possible with a bulk material handling system. We supply fully integrated conveying solutions for heavy construction and other projects, and then back them up with best-in-class support and service.
Contact us today. Our experts will work with you to determine if a conveyor system is right for your business. They will also develop a fully customized solution that meets your needs and budget today and is ready to grow with you into the future.
Sources
- Winston Shakantu, John Tookey, and Paul Bowen, “The hidden cost of transportation of construction materials: An overview,” Journal of Engineering, Design and Technology 1(1) (December 2003): 103-118 (link)
- Breno Gonçalves Cardozo Ribeiro, Wilson Trigueiro de Sousa, and José Aurélio Medeiros da Luz, “Feasibility project for implementation of conveyor belts in an iron ore mine. Study case: Fabrica Mine in Minas Gerais State, Brazil,” Rem: Rev. Esc. Minas 69 (1) (Jan-Mar 2016) (link)
- U.S. Department of Energy, “Mining Industry Energy Bandwidth Program: June 2007” (link)
- Witold Kawalec, Robert Król and Natalia Suchorab, “Regenerative Belt Conveyor Versus Haul Truck-Based Transport: Polish Open-Pit Mines Facing Sustainable Development Challenges” Sustainability 12(21) (November 2020) 1-15 (link)