Conveyors vs. Trucking & Hauling for Heavy Construction Projects
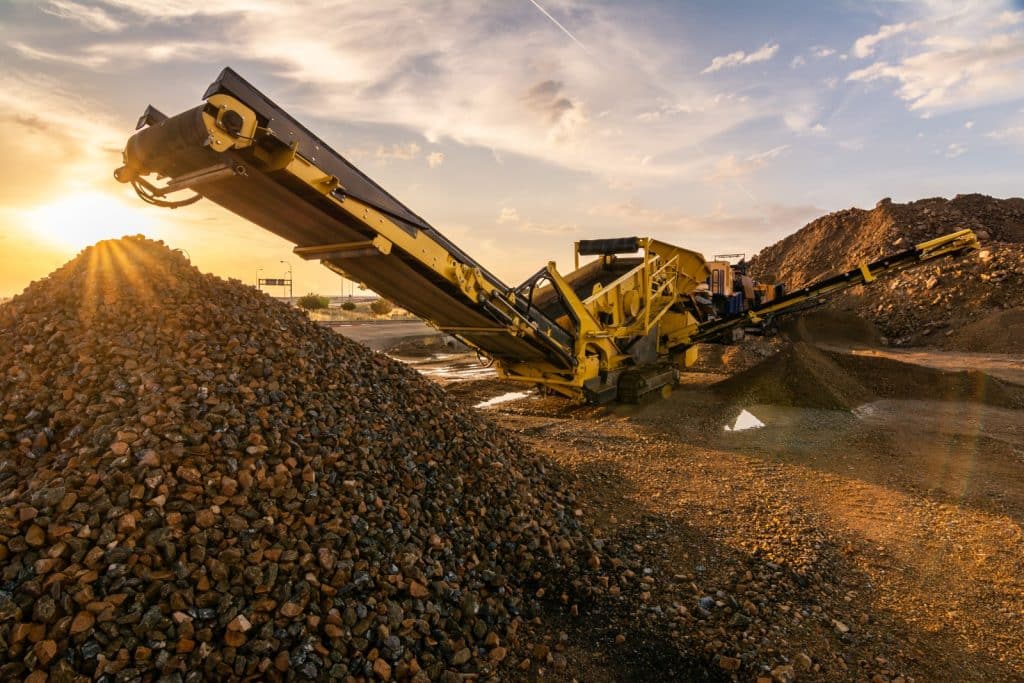
Suppose you’re a project manager planning a heavy construction or mining project. In that case, you’re likely already weighing the advantages of using fixed construction conveyors vs. trucking and hauling to transport your bulk materials.
It’s a critical decision that depends on a range of factors from project logistics, the type of material being moved, and the distance and terrain involved.
For many operators, haul trucks can be a tempting offer with low entry costs, few long-term commitments, and operational flexibility. That might not be the whole picture, however.
Below, we take a closer look at how to reduce material handling costs, specifically the advantages offered by modern, versatile overland conveyors vs. trucking and hauling in construction and mining. Read on, the results might surprise you.
WHY USE A CONVEYOR ON YOUR NEXT CONSTRUCTION PROJECT?
For large earthmoving projects, uncovering the true cost of transporting materials isn’t always straightforward, including its impact on your staff and local communities.
Let’s explore several practical reasons why choosing an overland conveyor vs. trucking and hauling for heavy construction and mining may make sense for your bottom line and beyond.
1. EFFICIENCY
The total purchase and installation cost of a conveyor system for your project can be hard to square with the straight-up cost of a trucking and hauling service. Look closer at your long-term operational costs for both and you’ll see conveyor systems pulling ahead in several key areas.
HAULAGE COSTS
If you’re planning or running a large construction or mining project, you already know that just getting bulk materials to where they’re needed can eat up a big chunk of your budget.
While estimates vary widely according to terrain, distance, project duration, and the materials being moved, one study of material transport costs across all types of construction projects found these could often comprise 40-60% of total expenditure.
CAPACITY
Another mining-specific study of overland conveyors vs. mining trucks found the cost per ton of haulage could drop between 30% and 75%, depending on the scale of the operation when conveyors are used to replace haul trucks.
Haul truck capacity also tops out at around 25 tons per trip, and vehicles must usually make the return journey empty. By contrast, medium-sized conveyors can often move up to 15,000 tons per hour.
ENERGY
A 2007 study by the Department of Energy found that diesel hauling accounted for 87% of the cost of material handling for major mining projects in the U.S. The same trucks delivered only 63% energy efficiency, measured in value delivered relative to the cost of fuel.
The same study found that electrically powered conveying systems were able to operate at close to 85% efficiency, potentially delivering big savings on a major project cost center.
Another study found an innovative “regenerative” conveyor design at a Polish open pit mine meant the operation was able to move coal almost twice as efficiently as with heavy haul trucks.
2. FLEXIBILITY
Think dump trucks give you more room to maneuver than conveyor systems when it comes to on-site challenges and changing conditions? Think again.
DRIVER SHORTAGES
Haul truck drivers have become harder to find as fewer younger people enter the market and experienced drivers age out. This long-term shortage is making it more challenging to move dirt, sand, gravel, and other materials on time.
The driver shortage means that simply putting more trucks on the road isn’t always an option for short-haul transfers. And, higher labor costs mean it now costs more to load, unload and operate large haul trucks.
Project managers can start solving the construction truck driver shortage by opting for conveyors over trucking and hauling. Conveyors can operate 24/7 with a much smaller workforce. Fixed conveyors also make sense where trucks must repeatedly haul the same route.
PORTABILITY
While dump trucks can get anywhere that is reachable by a reasonable dirt road, innovative suppliers like West River Conveyors offer more portable conveying options that can be repositioned as work locations shift.
Moveable conveyors are anchored with concrete blocks rather than secured to the ground, so they can be moved or transported as needed. Stacker conveyors, radial stacker conveyors, and transfer conveyors are fully movable options that provide more flexibility around transfer points.
SCALABILITY
With no fixed infrastructure footprint, trucks are usually considered a more flexible option than conveyors, able to shift load and unload points as your needs change and vary routes to suit local conditions. That flexibility is however limited by the relatively small load that an individual truck can carry.
In addition, scaling a truck haul operation means putting more vehicles on the road, adding incrementally to fuel and maintenance costs, labor needs, and environmental impact.
3. RELIABILITY
As investment and operating costs mount up, it’s important to be sure your outlay is going to deliver predictable, measurable returns. Reliable systems break down less often and are easier to fix and maintain.
DOWNTIME
Conveyor systems have fewer separate moving parts than trucks which means a reduced risk of breakdowns. Other conveyor benefits include reduced wear, optimized loading, and continuous motion, all of which let conveyors spend more time on the move and less time at a standstill due to maintenance and repairs.
Haul trucks are made up of multiple systems and are more likely to develop problems, especially if they are being heavily used, and unexpected failures can make getting parts and personnel to the breakdown point difficult and expensive. For conveyors, commonly needed parts and consumables can be pre-positioned close to where they are needed, so they can be switched out quickly when required.
WEATHER
Fleets can also be halted by snow, ice, flooding, or extreme temperatures. Conveyor systems, on the other hand, provide a straight-line connection between the source and destination.
They also require no road clearing or deicing and can operate 24 hours a day, seven days a week in all but the most extreme weather conditions.
OTHER DELAYS
Heavy-haul trucks often face restrictions on traveling after dark and the number of journeys per day through public areas. They can also be slowed down by traveling through congested urban areas. Even simply needing to cross one public highway can add significant delays over the lifetime of a project.
Conveyors, by comparison, typically avoid built-up areas and major roads, and, once set up, do not require further permissions or certifications. They run continuously at times when haul truck fleets might be stuck in neutral.
4. SAFETY
Safety should be a primary concern when evaluating haulage solutions. Accidents and injuries not only affect the lives of those involved, but they also take valuable workers off your project and can lead to increased downtime, liability issues, and reputational risk.
ACCIDENTS
According to OSHA (the Occupational Safety and Health Administration), approximately 75% of struck-by fatalities at worksites involve heavy equipment such as trucks or cranes.
Modern conveyors run continuously with few workers directly accessing them during operation. In fact, a conveyor system typically requires only half the workforce needed to run a fleet of trucks, putting fewer people at risk.
With less mobile equipment, reduced handling, and fewer on-site operations & maintenance staff, replacing short-haul trucks with conveyors helps eliminate safety risks and reduces your exposure to expensive equipment repairs and replacements.
LIABILITY
Bringing your haulage needs in-house with a conveyor means you won’t need to worry about whether a contractor is maintaining vehicles properly or drivers are violating their hours. That reduces your exposure to legal consequences and keeps safety standards firmly under your control.
5. ENVIRONMENTAL, SOCIAL & COMPLIANCE
Environmental and social impact reporting is now a best practice for large and small mining and construction companies. A project’s noise pollution, gas emissions, road wear, ecological damage footprint, and safety commitments must be weighted alongside profits. Here’s why a conveyor system may make it easier to meet your compliance targets.
NOISE
Haul trucks are noisy. Trucking sounds affect nearby workers and frustrate the public, especially if your project is in a populated area.
Conveyors are an excellent option for earthmoving when you’re concerned about keeping noise levels low. When you select the appropriate idlers, low-noise bearings, and conveying speed, you’ll find a conveyor system surprisingly quiet.
AIR QUALITY
For underground projects, such as mining or tunnel construction, conveyor systems have a significant advantage over trucking & hauling options. In addition to being safer and running quieter, conveyors emit few exhaust fumes. Less toxic fumes equate to less expenditure on air scrubbers and exhaust removal.
Overland conveyors are also cleaner and more efficient. Unlike trucks, a conveying system doesn’t throw stones or spread dust. Modern transfer chutes with conveyor belt skirting essentially eliminate dust and spillage, which is an advantage for any construction site.
WEAR & TEAR
Conveyors can move aggregate and other bulk materials quickly over challenging terrains, such as hills, rivers, and unstable ground. Your material transfer may require less road construction and avoid the vibration and damage to public streets sometimes caused by heavy hauling.
THE BOTTOM LINE: CONVEYORS VS. TRUCKS
Recent research supports the idea that modern, efficient conveyor systems can more than offset the apparent savings on short-haul trucking when total operational costs are considered.
Although upfront procurement, installation, and commissioning costs are typically higher, conveyor systems consistently outperform heavy haul trucking in terms of operational costs.
For example, research conducted in 2016 for an iron ore mine in Brazil found that the capital cost of using haul trucks to move material was just more than half of that of building a conveyor system with the same capacity.
Meanwhile, the operational cost of moving a ton of ore by conveyor was a quarter of that of trucks and produced 29% less carbon emissions.
For efficiency, flexibility, reliability, and safety over the long haul, it’s hard to beat the performance you’ll get from a quality conveyor system from a reliable provider like West River Conveyors.
AT WEST RIVER, WE’RE SHIFTING EXPECTATIONS
Heavy construction projects face unique challenges, from moving work locations to competing deadlines. As a project manager or estimator, getting the right quantities of aggregate or other bulk materials to where they’re needed is just one of the problems on your plate.
Modern conveyor systems are safe, efficient, and reliable and can be right-sized to your specific material-handling requirements. You’ll get a low-impact solution that delivers on your promises day in and day out.
At West River Conveyors, we build conveyor products that shift expectations about what’s possible with a bulk material handling system. We supply fully integrated conveying solutions for heavy construction and mining projects, and back them with best-in-class support and service.
If you’re looking for a smarter way to transport bulk materials, contact us today for a customized quote for a conveyor system that suits your needs.