How to Choose the Right Scrapers for Your Conveyor Belt
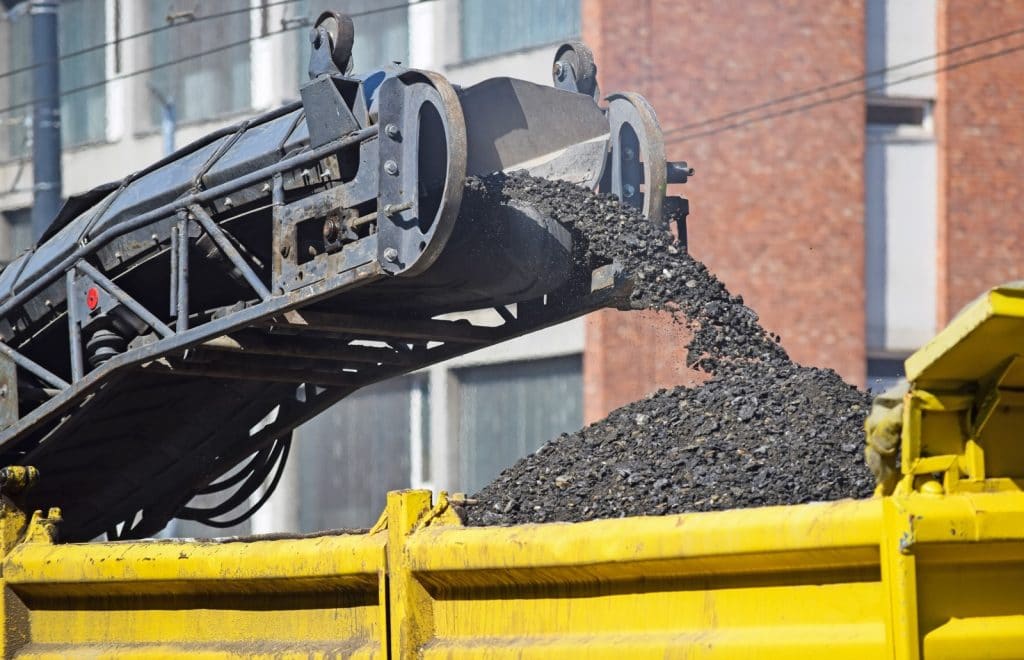
When properly set up, the right scrapers will extend the life of your conveyor belts while reducing maintenance and cleaning. Conversely, scrapers that are badly adjusted or not suited to the material being moved will wear the belt faster, limit the lifespan of your belts and leave the area around the conveyor dirtier than it should be.
Scraper systems can be as crude as a length of angle iron pressed against the belt. A better solution is an engineered mechanism that applies a constant load through a material that’s matched to what the conveyor is moving. Here’s some advice for getting it right.
WHY SCRAPE AT ALL?
Not all the material dropped onto the belt gets discharged. A proportion – how much depends on the material – stays on the surface and gets taken back on the underside. Some will drop off along the way and leave a mess. Some will instead cycle round and round, gradually building up until it falls off under its own weight. This carry-back is bad for your conveyor system. More specifically, it:
- Increases weight on the belt and thus the power drawn by the motor
- Increases belt loading through the extra weight
- Leads to uneven loads that strain the motor, reducer, and belt itself
- Causes mistracking, which accelerates belt wear
- Spreads dust and dirt that get into bearings and reduce component life
HOW AND WHERE TO SCRAPE
A scraper is a blade pressed against the belt surface. This knocks off material stuck to the belt. The force applied to the belt is a function of the material. Dry, granular materials stick far less so the scraper doesn’t need to be pressed as firmly against the belt as if it’s carrying a bituminous or tarry material.
The scraper should be applied where the belt is flat. The best place for this is at the head pulley where the drive is connected. Often this primary scraper is mounted at a 3 o’clock position relative to the pulley shaft.
A secondary scraper is used on the return side of the belt where it leaves the discharge pulley. This two-scraper arrangement effectively removes almost all material. Some conveyor operators like to have a third inner scraper to keep the underside of the belt clean.
OPTIMIZING SCRAPER LOAD
If the scraper isn’t set up to apply enough force to clean the belt you’ll get material carry-back, which the scraper is intended to avoid. Conversely, apply too much force and:
- Belt and scraper will both wear faster than is necessary
- The load on the belt and drive will be higher
- The scraper will heat up
- There’s an increased risk of snagging a tear and making it worse or catching and damaging a spliced joint
To avoid these problems every scraper needs an adjustment mechanism. The simplest are adjusted manually but better systems are either spring-loaded or use a counterbalance system. These ensure a constant load is applied. The best will ride over bumps and splices without being damaged or damaging the belt.
Whatever system is used, each scraper should be inspected daily for correct adjustment and operation.
SCRAPER SELECTION
Every scraper has two main parts: a blade that presses against the belt and a mechanism that holds it in place. Both should be appropriate to the material being conveyed.
A belt used for dry, granular material that doesn’t stick needs less load on the scraper and can therefore be lighter duty, perhaps with manual adjustment. A heavy sludge or tar that sticks to the belt needs the scraper to apply more force, which requires heavy-duty construction and ideally, a constant force mechanism.
A complete scraper system for a 30” belt should cost around $2,500.
The blade should be made from a material that deforms enough to avoid doing any damage but at the same time applies enough force to scrape away clingy material. It should also resist abrasion without softening excessively if it heats up. Some applications may also need water or chemical resistance.
For most applications, these characteristics are provided by a urethane blade. Scraper manufacturers produce urethane blades in durometer values of 70 to 90 Shore A. (That’s about as firm as a shoe sole or the leather in a belt, but not as firm as a golf ball.)
Blade length is important. While a 6” blade will work on a 24” diameter pulley, a 12” blade will last longer and do a better job. Poor quality blades can flip or twist, which makes them ineffective. Expect to pay $220 or more for a good 6” blade and $600 for one 12” long.
ADVICE ON CHOOSING THE RIGHT SCRAPER
A conveyor system with the wrong scrapers, or worse, no scrapers, is going to cost more to operate than one where belt cleaning has been addressed properly. There will be more wear and tear on the belt and other components, more cleaning will be needed around the structure, and it will consume more power.
As conveyor system experts, West River Conveyors is familiar with the selection and installation of scrapers and scraper blades. We carry primary and secondary scrapers and blades from several manufacturers. We can review your application, explain your options, and help determine what will work best. The result will be lower costs and longer-lasting belts.
For more advice on maintenance to reduce belt wear and tear, click below.