HOW TO CHOOSE THE RIGHT MINING CONVEYOR
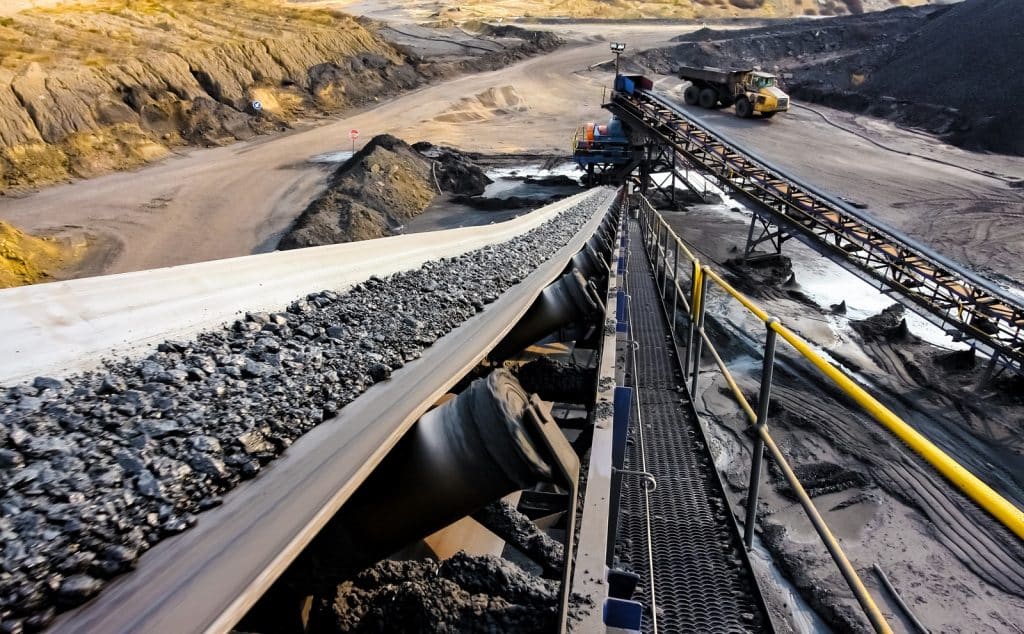
Haulage and transportation expenses can make up a significant portion of your mining project’s costs. Correctly designed and installed mining conveyors can slash your out-of-pocket operational costs, but only if you choose the best conveyor equipment for your application.
In this blog, we take a close look at what goes into selecting the right mining conveyor for your project. We’ll explore important factors to consider when choosing a conveyor, as well as lay out a set of best practices for your conveyor procurement and design process. Read on to learn more.
LONG GAME: HOW TO SELECT THE RIGHT MINING CONVEYOR
Conveyors play a critical role in many mining applications, providing cost-effective handling of almost any raw material while accessing areas other handling solutions cannot.
Although upfront investment is often significant, purpose-built conveyor systems outperform other alternative, such as haulage vehicles, by:
- Accessing hard-to-reach areas directly
- Limiting the need for manual handling and transfer of materials
- Improving safety and reducing environmental impact
- Lowering fuel and labor costs
In many cases, well-designed conveyor systems can significantly boost project throughput and increase overall handling efficiency for long-term returns on investment.
7 FACTORS TO CONSIDER WHEN CHOOSING A CONVEYOR
To deliver these benefits, your conveyor needs to be matched to your specific needs and project parameters by an experienced equipment provider. Here are some important things to keep in mind when considering how to design the right mining conveyor.
1. MATERIAL TYPE
The material you are handling will affect many aspects of your conveyor design, from belt material and troughing to the overall load capacity of your conveyor’s structure. Discuss with your equipment provider how the weight, friability, abrasiveness, and stacking characteristics of your material will affect conveyor design.
2. THROUGHPUT REQUIREMENTS
What throughput capacity do you require from your new equipment? Larger loads can dramatically increase efficiency but will require heavy-duty construction and more robust belt and drive characteristics, increasing your initial investment.
3. ENVIRONMENT
What sort of environment are you operating in? Will equipment be exposed to high heat, extreme cold, or dust and high winds? Corrosive conditions in very humid or salty environments may limit the life of exposed metal. Your supplier may recommend galvanized or stainless steel construction to increase equipment life and reduce maintenance needs.
4. DISTANCE AND TERRAIN CHARACTERISTICS
Conveyors can manage handling and transfer needs over just a few feet or many miles. For short distances steep inclines and descents may be manageable and cost-effective, but long-distance haulage may require more powerful drive equipment, increased footing, or additional transfer points to manage uneven ground or elevation changes.
5. SAFETY AND ENVIRONMENTAL FEATURES
Any project needs to meet or even exceed compliance with industry safety standards set by OSHA or the MSHA. Ensure your equipment has fencing to prevent unauthorized access and safety walkways and guarding to prevent falls and entrapment accidents. Add emergency stop controls and pull cords to shut down your line immediately in an emergency.
Good conveyor design should minimize the chance of spills during operation or an unexpected shutdown. Any project should also include comprehensive dust control measures to limit material loss and reduce respiratory hazards to your staff or nearby communities.
6. MAINTENANCE REQUIREMENTS
Designing your conveyor with robust materials and standardized parts can significantly reduce maintenance costs over the life of your equipment. Consider adding walkways and guarding to make access to critical equipment easier. Additionally, look at the cost involved in keeping an inventory of critical replacement parts on hand to reduce downtime.
7. BUDGET CONSTRAINTS
Your budget for new equipment is always limited, and conveyors require a larger upfront investment than other haulage options but deliver long-term benefits and ROI. Consider your needs and priorities carefully. Talk to your equipment supplier about how you can save by including more cost-effective materials and standardized parts in your design.
MATCHING YOUR CONVEYOR TYPES TO YOUR APPLICATION
Choosing the right type of conveyor or the best combination of equipment is essential to unlocking all the benefits that conveyor systems offer. Different types of conveyors are designed to handle specific tasks.
OVERLAND CONVEYORS
Overland conveyors are designed for long-distance material transport. They move large quantities of material over extended distances, often crossing rugged terrains and variable elevations to bring materials from distant sites to a central processing or distribution facility. They’re also designed to handle a wide range of material types.
UNDERGROUND CONVEYORS
Underground conveyors feature a more compact design and different mounting options for use in the confined spaces of underground mining operations. By automating the movement of materials to the surface, these conveyors reduce the need for manual labor and significantly improve safety underground.
PORTABLE TRANSFER CONVEYORS AND RADIAL STACKERS
Portable transfer conveyors and radial stackers are ideal for transferring material between longer-distance conveyors, stacking materials, or loading haulage trucks. Without fixed footing, these conveyors provide flexibility and mobility, allowing them to be repositioned as needed. They are particularly useful in aggregate and quarry operations and at temporary setups or sites.
BEST PRACTICES FOR CONVEYOR SELECTION
Here are six tips for getting your conveyor procurement process right.
Conveyor Best Practices Checklist | |
---|---|
Conduct a thorough needs assessment | Identify your specific requirements, including material type, throughput, and operating conditions, to ensure your conveyor meets your needs. |
Choose an experienced supplier | Choose an experienced supplier, like West River Conveyors, who knows about designing conveyors across all types of mining operations. |
Plan for future scalability | Design your conveyor system with the future in mind, allowing you to expand, upgrade, and even repurpose your equipment as your needs change. |
Prioritize maintenance and accessibility | Consider adding walkways, platforms, and special guarding to enable safe, easy inspection and maintenance, minimizing downtime and labor costs. |
Design for energy efficiency | Select energy-efficient motors and regenerative braking systems to make better use of the available power and reduce your energy overheads. |
Take safety seriously | Meet and exceed safety standards by including safety features such as emergency stop controls, dust mitigation, and proper guarding to protect your staff and local communities. |
MISTAKES TO AVOID IN CONVEYOR SELECTION
Conversely, you can ensure a smoother and more cost-effective design and installation process by avoiding the following common missteps:
- Overlooking maintenance requirements: A conveyor system that is difficult to maintain can lead to frequent downtimes and increased labor costs. Make sure the design includes easy access points and uses standard parts to speed up replacements.
- Underestimating environmental factors: Environmental conditions can significantly impact conveyor performance and longevity. Failing to plan for temperature, humidity, and corrosive environments increases maintenance costs and can shorten your equipment’s lifespan.
- Failing to match conveyor to application: Ensure that the chosen conveyor matches your material characteristics, load requirements, distance, and terrain.
- Neglecting safety features: Operators often underestimate the impact of accidents on their operations. Skimping on safety features can lead to accidents and regulatory fines. Your conveyor system must meet or exceed OSHA and MSHA standards.
WEST RIVER CONVEYORS: WITH YOU FOR THE LONG HAUL
Conveyor systems can offer short-term operation benefits and long-term return on investment when implemented properly. For most operators, installation involves serious capital investment that will add value for years to come.
There’s no substitute for experience when it comes to matching conveyors to your operating conditions and project goals. West River Conveyors is a recognized leader in supplying robust, effective conveying solutions for some of the toughest mining conditions.
With experience supplying coal, ores, salt, potash, aggregates, and sand, West River has on-the-ground expertise in your material needs and challenges. Talk to us about your handling, transfer, or long-distance transport needs. We’ll help design a safe, efficient, affordable, and scalable solution that will deliver value for the long haul.
Contact us today, or click below to learn about our fully customizable conveyor solutions.