MAXIMIZING THE LIFESPAN OF MINING CONVEYOR BELTS WITH PROPER CARE
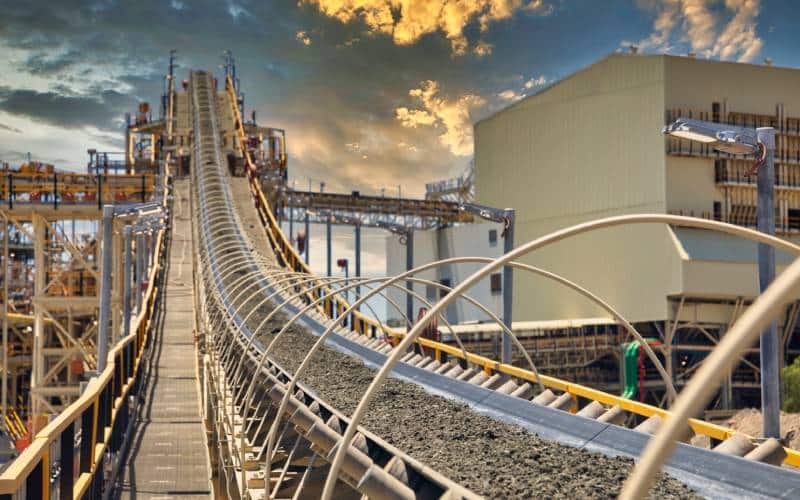
Mining conveyors are a marvel of modern engineering. They can withstand the rigors of moving thousands of tons of rock, sand, gravel, and aggregate to their final destination. However, like all complex machinery, mining conveyors require ongoing maintenance. This helps to ensure peak performance while reducing downtime as much as possible.
We put together this resource to help you understand how to keep your conveyors moving product efficiently for as long as possible.
KEY CONVEYOR BELT ISSUES AND HOW TO ADDRESS THEM
Proper maintenance and inspections are essential for preventing and addressing the most common conveyor belt issues. Regular upkeep improves safety, minimizes downtime, and extends the life of your equipment. Below are the three most critical issues to monitor and maintain.
Belt Mistracking – This occurs when the belt moves off-center, often caused by misaligned idlers and rollers, damaged pulleys, or faulty skirting. This issue can lead to wear, belt damage, and material spillage.
To prevent mistracking:
- Inspect for misaligned or locked idlers and rollers during regular maintenance.
- Look for damaged wing or tail pulleys and replace them as needed.
- Ensure chute structure skirting is intact and properly aligned.
- Address material overload, crooked splices, or worn vulcanized belt splices promptly.
Belt Slippage – This happens when the belt lacks proper tension or grip, often due to worn or improperly installed pulleys. This can cause motor strain and belt wear.
To mitigate slippage:
- Check for reduced lagging grip on head drive pulleys and replace them as needed.
- Inspect for material overload or misaligned components.
- Follow manufacturer specifications for proper belt tensioning.
Material Carry-Back – when material adheres to the belt instead of discharging properly, it can damage components reduce efficiency.
To handle carry-back:
- Use high-quality belt cleaners and scrapers suitable for your conveyor.
- Regularly inspect scrapers for cleanliness, proper tension, and alignment.
- Replace worn or malfunctioning scrapers with high-performance options for longer durability.
- Clean accumulated debris from return rollers and install dust containment systems to minimize buildup.
ROUTINE MAINTENANCE TIPS
Incorporating a structured maintenance plan ensures proactive issue resolution:
- Grease roller bearings to prevent lockup.
- Remove dirt or debris from the belt and components.
- Tag and lockout conveyors for safety before performing any cleaning or maintenance.
- Speak with workers to identify any operational issues noticed during shifts.
PERIODIC MINING CONVEYOR BELT MAINTENANCE
As-needed maintenance should focus on replacing worn or damaged equipment as quickly as possible. The most common areas include:
- Impact Cradles—These help minimize the force of falling material and prevent excessive belt wear and tear.
- Belt Repairs—Immediately perform belt repairs according to the manufacturer’s specifications. Mechanical fasteners are not a long-term solution for closing tears.
- Lagging—Replace non-ceramic lagging anywhere from 3-5 years.
- Power Module/Gearbox—After the initial break-in period, perform an oil change every 2,500 hours of service. Drain the reducer and flush it with kerosene. After cleaning the magnetic drain plug, refill the reducer to the proper level with the recommended lubricant.
- Bearings and Motor Replacement—Keep track of hours of operation and replace as per the manufacturer’s recommendations.
By addressing these conveyor issues regularly, you can reduce wear and tear, improve efficiency, and ensure the longevity of your conveyor systems.
HOW TO MAXIMIZE THE LIFESPAN OF MINING CONVEYOR BELTS
Conveyor belts are a critical component of any material handling operation. Besides the routine maintenance practices described above, proactive strategies are vital in reducing the risk of belt failure and optimizing long-term performance. Implementing the following measures will help avoid costly repairs and unplanned downtime.
REGULAR BELT ALIGNMENT
Mistracking is a significant cause of belt damage. Even small misalignments can lead to belt edge wear, spillage, and increased load on the belt. Utilize automatic belt tracking devices or invest in remote monitoring systems to detect and correct mistracking issues early.
LOAD MANAGEMENT
Excessive material loading can stretch or deform belts, particularly in concentrated areas. Ensure balanced material flow across the belt to avoid localized stress points that lead to premature failure. Monitoring systems can help detect uneven loading and allow adjustments in real time to keep belts operating efficiently.
FREQUENCY OF LOADING
Shorter belts tend to experience more frequent impact at loading points due to the smaller distance the material travels on each cycle. This can contribute to accelerated wear. Optimizing the loading frequency and ensuring even distribution across the belt can help prolong its service life.
PREVENTATIVE MAINTENANCE FOR MINING CONVEYOR CHECKLIST
The checklist below provides a structured approach to preventive maintenance and ensures efficient operation and a longer lifespan.
DAILY MAINTENANCE
- Perform visual inspections of the entire conveyor system for:
- Lodged or stuck components
- Faulty electrical systems
- Structural damage due to accidents or weather
- Rocks or foreign debris on the belt (ensure the conveyor lockout).
- Belt wear, nicks, or cuts
- Unusual noises or vibrations
- Loose bolts, nuts, or other foreign objects
- Check for material carry-back and inspect:
- Scrapers for wear, improper installation, or incorrect sizing (ensure both primary and secondary scrapers are functioning properly)
- Scraper position, cleanliness, and tension
- Inspect for belt slippage and mistracking by checking for:
- Misaligned idlers or locked rollers
- Damaged wing or tail pulleys
- Faulty chute structure skirting or leaks
- Material overload on the belt
- Grease roller bearings to prevent lockup.
- Clean and inspect scrapers; adjust the tension to ensure even wear.
WEEKLY/MONTHLY MAINTENANCE
- Inspect for and correct belt mistracking by checking for:
- Misaligned, dirty, locked, or frozen idlers and rollers
- Material overload or faulty chute structure skirting
- Worn or crooked splices
- Damaged or broken idlers
- Check for belt slippage by inspecting:
- Lagging on the head drive pulley and replacing as needed
- Proper pulley installation and grip
- Inspect for material carry-back and check:
- Scraper quality and installation
- Dust containment systems at transfer points (to prevent equipment damage and minimize health risks)
- Clean up any dust accumulation.
AS-NEEDED MAINTENANCE
- Replace worn or damaged components, including:
- Idlers and rollers (check for freezing, misalignment, or dirt accumulation)
- Impact cradles (to reduce wear from falling material)
- Belts (repair tears promptly and avoid using mechanical fasteners)
- Lagging (replace every 3-5 years unless ceramic)
- Scrapers (opt for high-performance replacements)
- Dust containment systems (clean or replace regularly)
- Perform oil changes on power modules/gearboxes after the initial break-in period. Repeat every 2,500 hours of service. Flush the reducer with kerosene and clean the magnetic drain plug.
- Track hours of operation for bearings and motors and replace them according to manufacturer’s recommendations.
PREVENTIVE STRATEGIES FOR BELT LONGEVITY
- Ensure proper selection based on material type, load size, and speed.
- Consider the length: Longer ones experience less frequent impacts and wear more slowly than shorter ones.
- Optimize transfer point design to minimize regular and oversized material impact.
- Regularly align belts to prevent mistracking and uneven wear.
- Monitor load distribution to avoid localized stress.
- Install automatic tracking devices or remote monitoring systems to detect mistracking issues early.
- Install primary and secondary cleaning systems to reduce material carry-back.
- Manage loading frequency: Optimize the frequency of material loading to prevent excessive wear.
Remember that the material your conveyor carries can affect the recommended maintenance schedule. For example, when moving highly corrosive material, focus your inspection and maintenance on areas prone to corrosion. Dust-related concerns should prioritize component material, type of coating, type of bearings, and seals.
CONTACT THE CONVEYOR BELT EXPERTS
Regular maintenance is key to maximizing the efficiency and lifespan of your conveyor belts. As your system wears over time, it’s essential to have reliable parts ready for replacement to avoid unnecessary downtime.
At West River Conveyors, we offer high-quality replacement components tailored to your needs. Our dependable service and top-tier products are designed to ensure your operations stay on track.