UNDERSTANDING AND EXTENDING THE LIFE OF YOUR CONVEYOR COMPONENTS
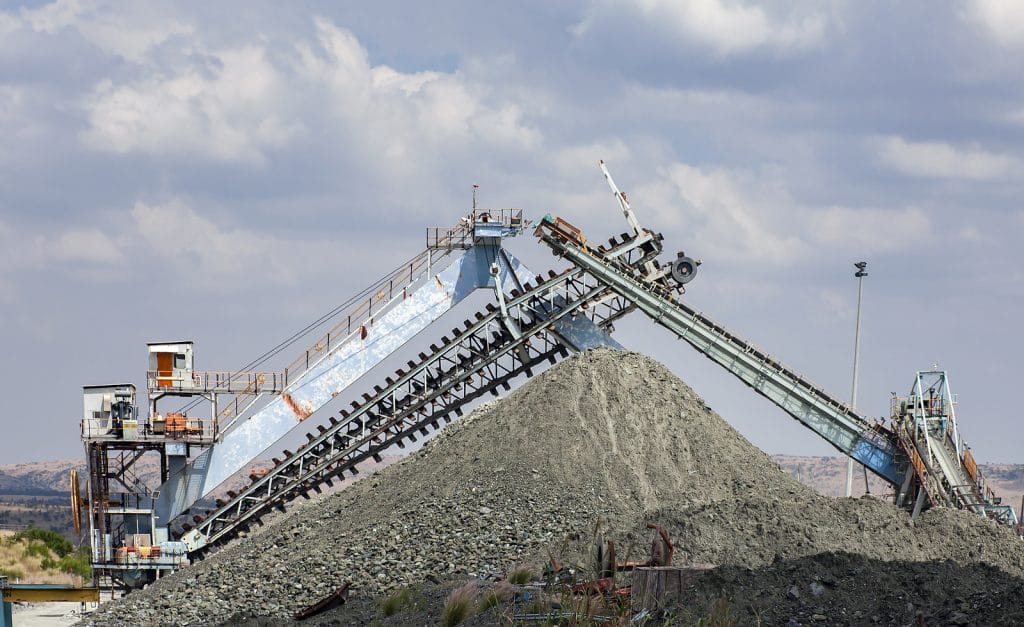
A mining conveyor—or any other conveyor used for moving rock, ore, or aggregate—represents a substantial investment. It needs to work hard, and stoppages for maintenance or repairs are expensive.
West River Conveyors engineers conveyor systems for the harsh environments they’ll be placed into, but there’s no avoiding wear and the need to replace mining conveyor belt components periodically.
Prolonging the life of major components reduces downtime and repair work, which leads to savings. As experts in conveyors for moving rock and aggregate, West River has the experience to advise on the most cost-effective ways of extending component life.
WHAT IS A MINING CONVEYOR?
A mining conveyor transports thousands of tons of ore and other raw materials from the mine to an endpoint. Unlike a fleet of expensive and polluting trucks, it requires very little manpower to operate.
A conveyor for a mine consists of a belt that’s stretched between two or more pulleys that are powered by a gas or electric motor. The belt is constructed out of highly durable and sometimes non-flammable materials to ensure long service life.
WHAT IS A CONVEYOR GEARBOX?
A mining conveyor gearbox is a mechanical device that transmits power and torque from the motor to the conveyor system. It allows the conveyor to move heavy loads at set speeds.
Gear boxes for mining conveyors utilize heavy-duty components and are reliable, durable, and able to withstand harsh mining environments. Every mining operation has unique challenges and West River Conveyors can engineer a conveyor gearbox to meet your specific requirements.
MINING BELT CONVEYOR COMPONENTS
In addition to the structure, which shouldn’t suffer much wear, the main mining conveyor belt components to consider for extending their lifespan include:
- Rollers & Idlers
- Pulleys
- Power Modules/Motors
- Gearboxes
- Scrapers
- Transfer Chutes & Rock Boxes
- Conveyor Belts
Each one has a typical or expected lifespan, which can be shortened through rugged use or extended by careful component selection and ongoing maintenance. Check out our Daily and Periodic Maintenance for Conveyors and Parts Guide.
ROLLERS & IDLERS
A typical material-handling conveyor could have hundreds or thousands of roller assemblies supporting the belt. The main parts of an idler are the bearings at each end and the shell that the belt rides on. Bearing problems increase the load on the motor, which raises energy costs and reduces belt life.
The biggest issue with idler bearings is the pitting of the raceway. This is caused by shock loads and grit or dirt contamination.
L10 life (the time after which 10% of the bearings will fail) of quality idler bearings is usually 50,000 hours or 5-7 years. However, this depends on the environment, belt speed, and cleanliness. To extend bearing life:
- Run the belt slower (understanding that this might not be practical)
- Use bearings fit for the environment (dust-excluding seals are prerequisites)
- Lubricate properly
The biggest cause of shell wear is the impact of a dirty belt. Shells should last 7-10 years but less if belt scrapers aren’t properly adjusted and maintained.
Idler roller conveyors, or idler rollers as they’re more commonly known, are cylinders that run the entire length of the conveyor belt. They’re located under the belt, and their job is to support the weight of the materials, assist in smooth belt movement, and maintain belt tracking.
There are many different types of idler rollers, including:
- Rubber Screw Idler Rollers
- Tapered Idler Rollers
- Rubber-Coated Idler Rollers
- Plain Idler Rollers
- Rubber Disc Idler Rollers
- Steel Screw Idler Rollers
PULLEYS
With regular lubrication and replacement of lagging, pulleys should last ten years or more. Centralized lubrication systems are available, but many belt operators find pressurized grease containers on zerk fittings more cost-effective.
Lagging protects the pulley shell from damage and increases friction at the conveyor drive pulley. Rubber is often used with a smooth finish on non-drive pulleys and a grooved or herringbone pattern on the drive.
Lagging typically needs replacing after 3-5 years of use. Keeping belt scrapers functioning correctly helps reduce wear, but the best option is to install ceramic lagging for longer life. Ceramic lagging is particularly effective when conveying abrasive material simply because it can withstand more abuse.
Ceramic lagging takes various forms. It’s available with a smooth surface or dimpled for additional friction and bonded to rubber or directly onto the pulley shell.
POWER MODULE & GEARBOX
The power module is a combination of the motor and gearbox. It’s an expensive unit, and it makes sense to extend its life as much as possible. Cared for correctly, it should provide 20 years or more of service.
The biggest factor in achieving and exceeding this life is proper lubrication. This begins with the first fluid change, which you should perform after two weeks of use. After the initial break-in period, change the oil every 2,500 hours of service. This would be every four months if it’s running 24×7.
At every oil change, drain the reducer and flush it with kerosene. Remember to clean the magnetic drain plug before refilling it to the correct level with a new lubricant of the grade/viscosity specified by the gearbox manufacturer.
SCRAPERS
Though often neglected, scrapers play an important role in extending the life of mining conveyor belt components. When correctly adjusted, the scraper keeps the belt clean, which minimizes shocks to and wear of idlers and pulleys.
Scrapers take many forms, but most need periodic adjustment of tension or load on the belt. Too much increases belt wear and drive friction, while too little leaves material on the belt. Your scraper manufacturer can advise on the optimum settings.
TRANSFER CHUTES/ROCK BOXES
Rock boxes, and to a lesser extent transfer chutes, are expected to wear in use. For this reason, rock boxes are usually lined with sacrificial material that needs replacing periodically.
From the extended belt component life perspective, the most crucial factor with rock boxes and transfer chutes is proper alignment over the belt. The material should be deposited into the center of the belt and not to one side. Correct deposition helps extend the life of the belt and the idlers.
CONVEYOR BELTS
The belt is the heart of the conveyor system. While it couldn’t function without the components mentioned above, belts should provide at least three years of reliable service. Speed, length, loading, and strength are key factors that influence belt life.
Click here for more detail on these and additional life-extending tips.
Belt structure and covers should always be appropriate to the material you’re conveying. An experienced conveyor manufacturer like West River Conveyors can help you choose what is best for your application.
GET EXPERT HELP WITH MINING CONVEYOR BELT COMPONENTS WHILE SAVING MONEY
Proper care and maintenance of a conveyor carry a cost, but it’s usually insignificant when compared to the expense of unplanned downtime. Prolonging the life of mining conveyor belt components provides an ROI through lower expenditure on spares and replacements and reduced downtime.
West River Conveyors can advise on the most appropriate types of components for your application or industry and will help you maximize the life you get from them.
Learn more about how to prevent common conveyor belt problems.